Seis maneiras de evitar defeitos em soldas
As precauções discutidas aqui podem ajudar a minimizar custos desnecessários, auxiliar em uma maior produtividade e fazer com que a operação de soldagem permaneça competitiva
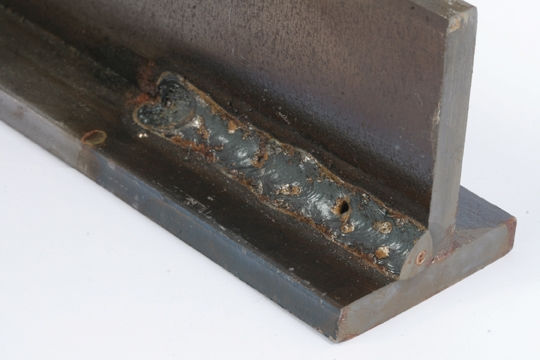
Os defeitos de solda podem ocorrer de várias maneiras, sendo geralmente causados por simples descuidos durante a operação de soldagem. Em muitos casos, esses descuidos resultam da falta de treinamento adequado com relação às técnicas necessárias para a soldagem de um material em particular ou de um determinado tipo de junta.
Independentemente da razão, o resultado é o mesmo. Problemas como trincas a quente e a frio, fusão incompleta das paredes laterais, inclusão de escória ou sobreposição podem ocorrer, causando atrasos na produção e interrupções para o retrabalho das peças.
Todos esses problemas provocam um efeito adverso na produtividade e lucratividade geral da operação de soldagem. Quando uma peça é rejeitada devido a um defeito de solda, a empresa incorre em tempo, mão-de-obra e despesas extras para identificar e corrigir o problema. Além disso, a empresa também corre um risco maior de comprometer a segurança, caso o defeito ocorra em uma aplicação crítica.
Entretanto, os operadores de soldagem podem tomar certas precauções para se protegerem contra esses problemas. Tais precauções podem ajudar a minimizar custos desnecessários, auxiliar em uma maior produtividade e fazer com que a operação de soldagem permaneça competitiva.
A seguir são apresentadas seis dicas fundamentais para evitar defeitos de solda:
1. Utilize metais de enchimento de baixo hidrogênio sempre que possível
A maioria dos fabricantes de metais de enchimento oferece uma variedade de produtos, particularmente arames tubulares e eletrodos revestidos, que produzem baixos níveis de hidrogênio difundível.
Ao soldar aços ferríticos (ou com base em ferro), o uso desses metais de enchimento pode ser uma boa defesa contra defeitos de solda causados por trincamentos induzidos por hidrogênio, também chamados de trincamentos a frio. Esse tipo de defeito ocorre geralmente horas ou dias após o esfriamento da solda e é o resultado da tensão residual do material de base quando este é contido ao longo da solda, mais a presença do hidrogênio na solda. Materiais mais espessos são mais propensos a defeitos, já que tendem a criar áreas de alta contenção e podem funcionar como dissipadores de calor que levam a rápidas taxas de resfriamento – a condição ideal para o hidrogênio coalescer e elevar as tensões residuais da solda. Os aços de alta resistência e as aplicações com juntas contidas também são propensas a defeitos de solda por trincamento a frio.
📷
Os metais de enchimento com um designador H4 ou H8 são boas escolhas para evitar defeitos de solda associados com o trincamento a frio, já que minimizam a quantidade de hidrogênio adicionado à solda inicialmente e, com isso, a oportunidade de causar um trincamento durante o resfriamento dela.
Esses metais de enchimento contêm, respectivamente, menos de 4 ou 8 ml de hidrogênio por 100 g de metal.
Em certos casos, utilizar metais de enchimento com um sistema básico de escória também pode ajudar a reduzir o risco de defeitos de solda por trincamento a frio. Esses metais de enchimento geralmente contêm elevados níveis de removedores de hidrogênio, incluindo flúor, sódio e cálcio, que podem combinar-se com o hidrogênio para retirá-lo de uma solda em resfriamento.
2. Tome cuidado com o ajuste e o projeto da junta
O ajuste adequado da peça e um bom projeto de junta são pontos fundamentais para evitar defeitos de solda, particularmente aqueles associados ao trincamento a quente. Se houver problemas em algum desses pontos, não é raro que o operador de soldagem tente compensa-los criando um cordão de solda mais largo para fundir o metal. O perigo em fazê-lo, entretanto, vem do fato de que a solda resultante poderá ficar com uma garganta muito fina, tornando-a fraca e gerando tensão em sua parte central. O resultado geralmente é uma condição chamada de trincamento em forma de cordão, um tipo específico de trincamento a quente que aparece imediatamente após o resfriamento da solda.
Um bom procedimento, quando possível, é projetar a junta de modo que o operador de soldagem tenha acesso fácil à raiz. Fazer isso garantirá uma proporção adequada entre a profundidade e a largura do cordão. Uma faixa adequada para essa proporção é uma profundidade de 0,5:1 para 2:1 da largura.
3. Trate corretamente o material antes e após a soldagem
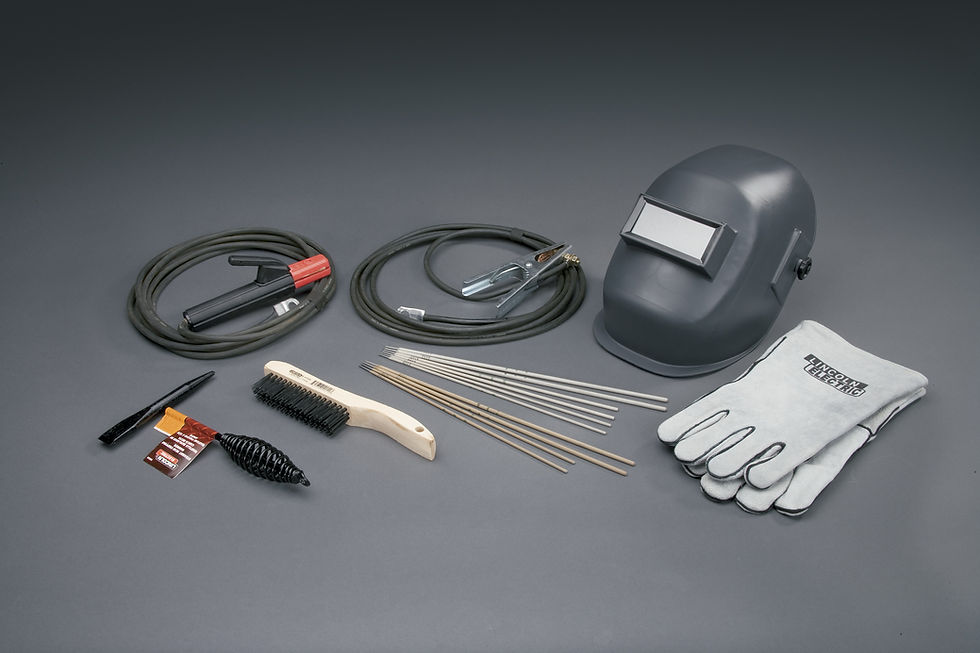
Alguns materiais são particularmente suscetíveis a defeitos de solda por trincamento, incluindo aços de alta resistência, que possuem um elevado teor de carbono e/ou de liga. Devido ao fato de esses materiais serem menos dúcteis, eles tendem a gerar tensões residuais no metal base e na solda acabada, durante o processo de resfriamento. Esses aços também são muito mais propensos a formar martensita na zona termicamente afetada quando são resfriados mais rapidamente.
A formação de martensita cria áreas na estrutura dos grãos onde o hidrogênio pode ficar armazenado, causando, como resultado, o trincamento. É importante pré-aquecer sempre tais materiais durante o tempo e à temperatura recomendados, de acordo com o procedimento de soldagem, para garantir que o calor se distribua uniformemente por toda a peça. O pré-aquecimento evita o resfriamento rápido e também ajuda a manter uma estrutura de grãos interna mais dúctil (perlítica) na zona termicamente afetada. Isso também limita as tensões de encolhimento do material e ajuda a reduzir os casos de formação de martensita.
Do mesmo modo, quando recomendado por um determinado procedimento de soldagem, deverá ser realizado o tratamento térmico posterior à soldagem. O tratamento térmico alivia as tensões residuais e libera hidrogênio difundível da solda, para evitar defeitos por trincamento a frio.
4. Escolha as resistências adequadas para o metal de enchimento e o material base
Selecionar a resistência adequada do metal de enchimento também poderá ajudar a minimizar o risco de defeitos de solda. A maioria das aplicações exige a correspondência entre a tensão ou resistência do metal de enchimento com a do metal base. As resistências devem estar o mais próximo possível uma da outra e ser selecionadas como aplicáveis aos requisitos de projeto da aplicação. Se estiver soldando um material de baixa resistência sobre um de resistência mais elevada, sempre combine o metal de enchimento com o de baixa resistência, já que isso permitirá maior ductilidade e ajudará a minimizar o risco de trincamento.
Ao fazer certas soldas de filete ou soldar uma aplicação que exija apenas a penetração parcial da junta, pode ser melhor escolher um metal de enchimento com resistência menor em relação ao material base. Fazer isso poderá minimizar as tensões residuais da solda acabada. 5. Implemente um sistema de armazenagem adequado, bem como procedimentos de manuseio apropriados para o metal de enchimento
Para evitar que os metais de enchimento acumulem umidade, poeira, detritos ou óleo que possam levar à sua contaminação e, eventualmente, causar defeitos da solda, é fundamental seguir os procedimentos
adequados de armazenamento.
Armazenamento Armazene os metais de enchimento em um local seco, em sua embalagem original, até que estejam prontos para ser utilizados. O ideal é manter a área de armazenagem à mesma temperatura da célula de soldagem, para evitar a condensação que ocorre ao mover-se de uma área fria para outra quente, o que faz com que o metal de enchimento absorva umidade.
Permitir que o metal de enchimento enchimento se aclimate à temperatura do ambiente de soldagem antes de abrir sua embalagem também poderá protegê-lo contra a absorção de hidrogênio. Os operadores de soldagem sempre devem usar luvas ao manusear o metal de enchimento, para protegê-lo da umidade das mãos. Além disso, quaisquer rolos abertos devem ser cobertos com um saco plástico quando não estiverem em uso. Fazer isso protegerá o metal de enchimento do acúmulo de contaminantes do ar que possam levar a uma poça de solda de má qualidade e/ou um defeito.
Ainda mais: as empresas nunca devem instalar estações de esmerilhamento próximas a uma área onde rolos de metal de enchimento estejam presentes, já que as partículas podem acumular-se no arame, causando potenciais inclusões na solda. Ao utilizar eletrodos revestidos, siga sempre os procedimentos adequados de armazenamento e de recondicionamento antes da soldagem.
6. Forneça treinamento adequado
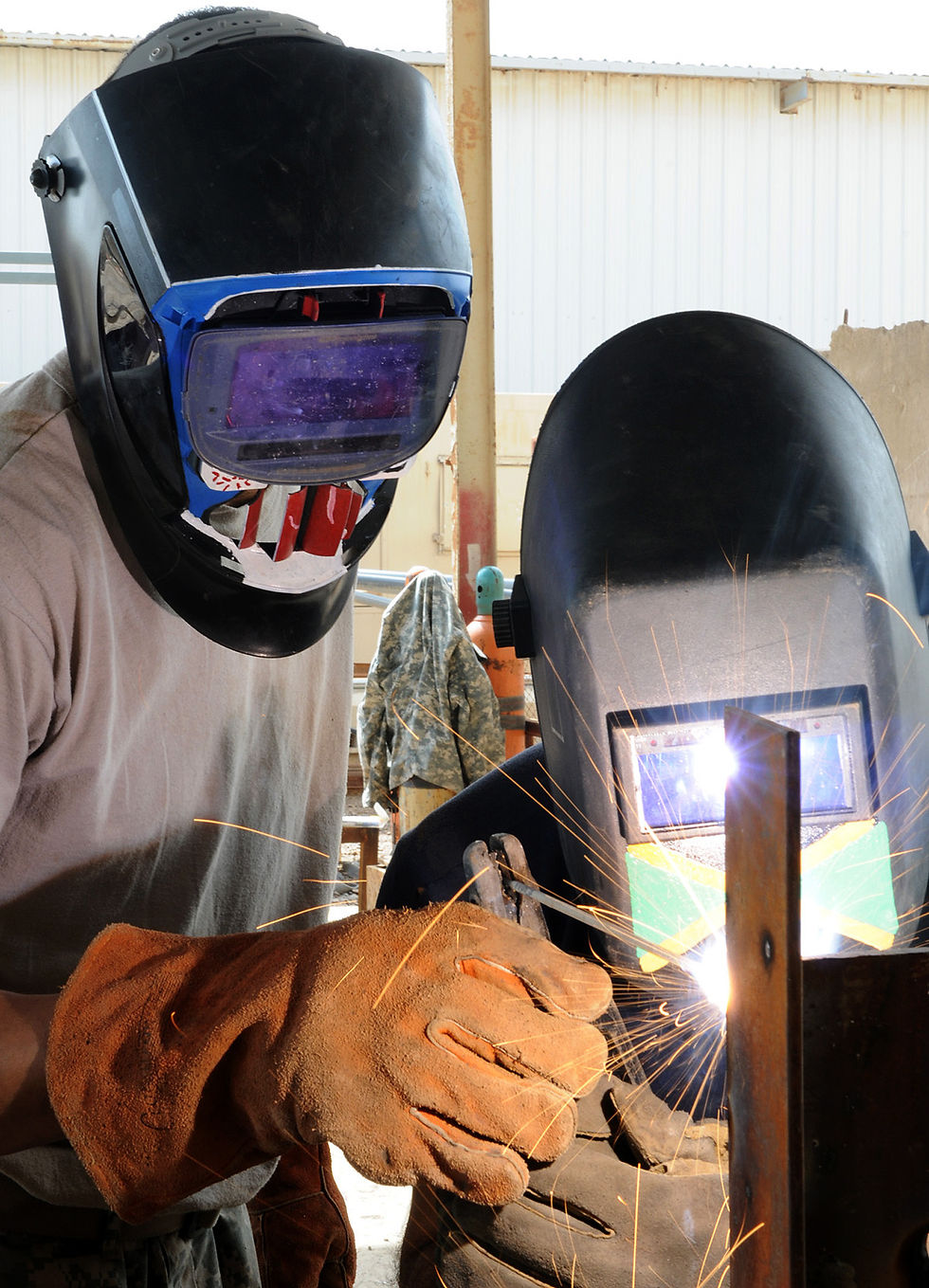
É impossível enfatizar suficientemente a importância do treinamento como primeira linha de defesa contra defeitos de solda. O treinamento adequado ajuda na aquisição de boas técnicas de soldagem, bem como da habilidade para tomar decisões acertadas que afetarão positivamente a operação de soldagem.
Os operadores de solda devem ser treinados para seguir sempre o procedimento de soldagem recomendado e investigar as causas comuns de defeitos de solda, como a mordedura, as inclusões de escória ou a porosidade, que podem levar a defeitos. Eles também devem ser treinados para cumprir com os requisitos especiais das ligas com as quais venham a trabalhar. Verifique com um distribuidor de soldagem local ou um fabricante de solda (ou de metal de enchimento), para conhecer as oportunidades de treinamento.
Eles podem frequentemente ajudar no treinamento para soldadores iniciantes, assim como na continuidade da formação. Se os recursos permitirem, as empresas podem considerar a implantação de seus próprios programas de treinamento. Por fim, os operadores de soldagem que seguirem os procedimentos e se ajustarem às várias facetas da operação de soldagem terão boas chances de alcançar a qualidade de solda desejada, além de evitar defeitos.
POST ORIGINALMENTE PUBLICADO EM http://www.metalica.com.br/pg_dinamica/bin/pg_dinamica.php?id_pag=797
コメント